Cement plants are traditionally associated with high energy consumption and high emissions, but the development pattern of Lafarge Shui On Cement in China has set a good example of a circular economy to reduce pollution and save power.
A sludge usage project to make cement began at Nanshan Cement Plant in Chongqing of Lafarge Shui On in September. The project was jointly developed by Lafarge Shui On and Chongqing Environmental Protection Bureau. With an investment of 6.5 million yuan, it consumes 36,000 tons of sludge from the local sewage treatment plant every year, while the cement production of Nanshan Plant in 2007 has exceeded 2 million tons.
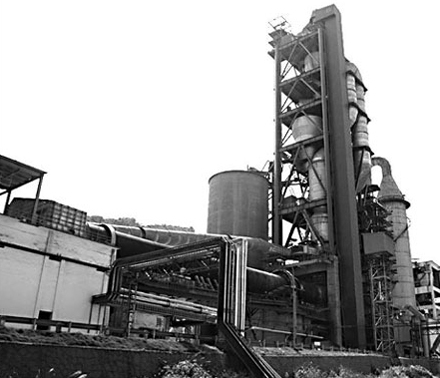
|
Nanshan Cement Plant of Lafarge Shui On in Chongqing. |
In the past sewage sludge has traditionally been buried in a local sewage treatment plant's landfill, but under the new project the sludge is taken from the sewage plant and processed into a raw material to produce cement. The sewage treatment plant pays Nanshan Cement Plant 100 yuan for every ton of the sludge it takes away. The cost of cement production is reduced and pollution caused by landfill disposal is also reduced.
"Using sludge makes the cement no different than before," a technician of Nanshan Cement Plant says in front of a rumbling cement kiln.
The sludge to cement process was first developed at Lafarge cement plants in France in the late 1990s and it's also currently being used in Japan and South Korea. "Lafarge is willing to bring our technology and experiences into China," says Bruno Lafont, the Chairman and CEO of Lafarge Group.
However, "such an undertaking is rarely seen in Chinese cement plants nowadays," says Deputy Secretary General of China Cement Association, Zhang Jianxin. "Lafarge's innovation has set a good example of a circular economy system in China."
Along with the sludge usage project, a waste heat recovery (WHR) project has also begun at the Nanshan Cement Plant.
The 82 million yuan project can meet 30 percent of the total electricity consumption of the Nanshan plant. It is predicted that the investment will be paid off within three years.
"The market price of electricity is 0.5 yuan per kWh, but our cost to produce a kWh of electricity is merely 0.1 yuan," he says.
Waste heat accounts for 30 percent of all the heat consumed during a significant portion of the cement making process. The WHR project will annually save 45 million kWh by recovering the waste heat from the cement kilns into power through a steam turbine, reducing carbon dioxide emissions by 70,000 tons. In addition to the Nanshan project, Lafarge Shui On has invested in five WHR projects in Sichuan and Yunnan.
WHR technology is also being used in other Chinese cement plants.
Anhui Conch Cement Co Ltd is the largest Chinese cement enterprise. By the end of 2007, the installed capacity of its WHR projects reached 168,900 kWh, accounting for 31 percent of the overall capacity of the entire Chinese cement industry. Anhui Conch plans to put another 19 WHR projects into operation during 2008, producing 3.79 billion kWh of electricity every year. In other words, 1.36 million tons of standard coal and 1 billion yuan in costs can be saved annually.
Henan province is now requiring that new suspension preheater (NSP) cement production lines with a daily production capacity of 5,000 tons and above must be equipped with WHR facilities.
The National Development and Reform Commission (NDRC) hopes that 40 percent of the NSP cement production lines in China will use WHR equipment by 2010. At that time, the annual electricity produced by WHR projects will reach 8.93 billion kWh.
Since 1985 China's cement production was the highest in the world for 21 consecutive years, accounting for 48 percent of the global annual output. Statistics from the NDRC show cement production in China during the past eight months reached 887 million tons.
The cement industry also consumes 15 percent of all the coal burned in China. Currently, China's carbon dioxide emission rate ranks second in the world.
According to the 11th Five-Year Plan for the Chinese cement industry from 2006 to 2010, the energy consumption of each ton of cement should be reduced by 25 percent compared with the previous five years.
(China Daily November 3, 2008)